In the world of industrial manufacturing, precision, speed, and durability are non-negotiable. One technology that has transformed industries like automotive, packaging, medical devices, and textiles is radio frequency (RF) welding. It offers a fast, reliable, and cost-effective solution for joining various plastic materials with precision and strength. If you're in the market for a welding solution or are simply curious about this process, this guide will give you a comprehensive understanding of radio frequency welding machines, their components, and the benefits they bring to the table.
What is Radio Frequency Welding?
Radio frequency welding (RF welding), also known as high-frequency welding, is a process where radio waves are used to generate heat to melt and bond plastic materials together. Unlike traditional welding methods, which use heat from an external source, RF welding uses electromagnetic energy to create an electric field between two electrodes. This field causes the plastic to heat and melt at a specific frequency, enabling the materials to fuse at the desired welding points.
This technology is ideal for materials like polyvinyl chloride (PVC), PTFE, ETFE, and PU, which are commonly welded in various industries. The RF weldability of these materials makes them suitable for complex shapes and large-scale production runs.
How Does Radio Frequency Welding Work?
At its core, the RF welding process relies on a specialized machine known as an RF welder. Here's how the process works:
- Material Preparation: The plastic materials to be welded are placed in the RF welding machine. These materials can be in the form of sheets, films, or custom-designed parts.
- Electromagnetic Energy Application: The machine generates radio frequency energy, which is applied to the plastic. The high-frequency waves penetrate the materials, causing the molecules in the plastic to oscillate and generate heat.
- Melting and Bonding: The heat generated from the radio frequency causes the plastic at the joint to melt, while the rest of the material stays cool. The sealing dies are then used to compress the welded areas, creating a solid, permanent bond.
- Cooling: Once the material is melted and the bond is formed, the RF welding equipment typically cools the plastic rapidly to maintain the integrity of the weld.
This process ensures that the welding process is both consistent and highly accurate, even for complex shapes.
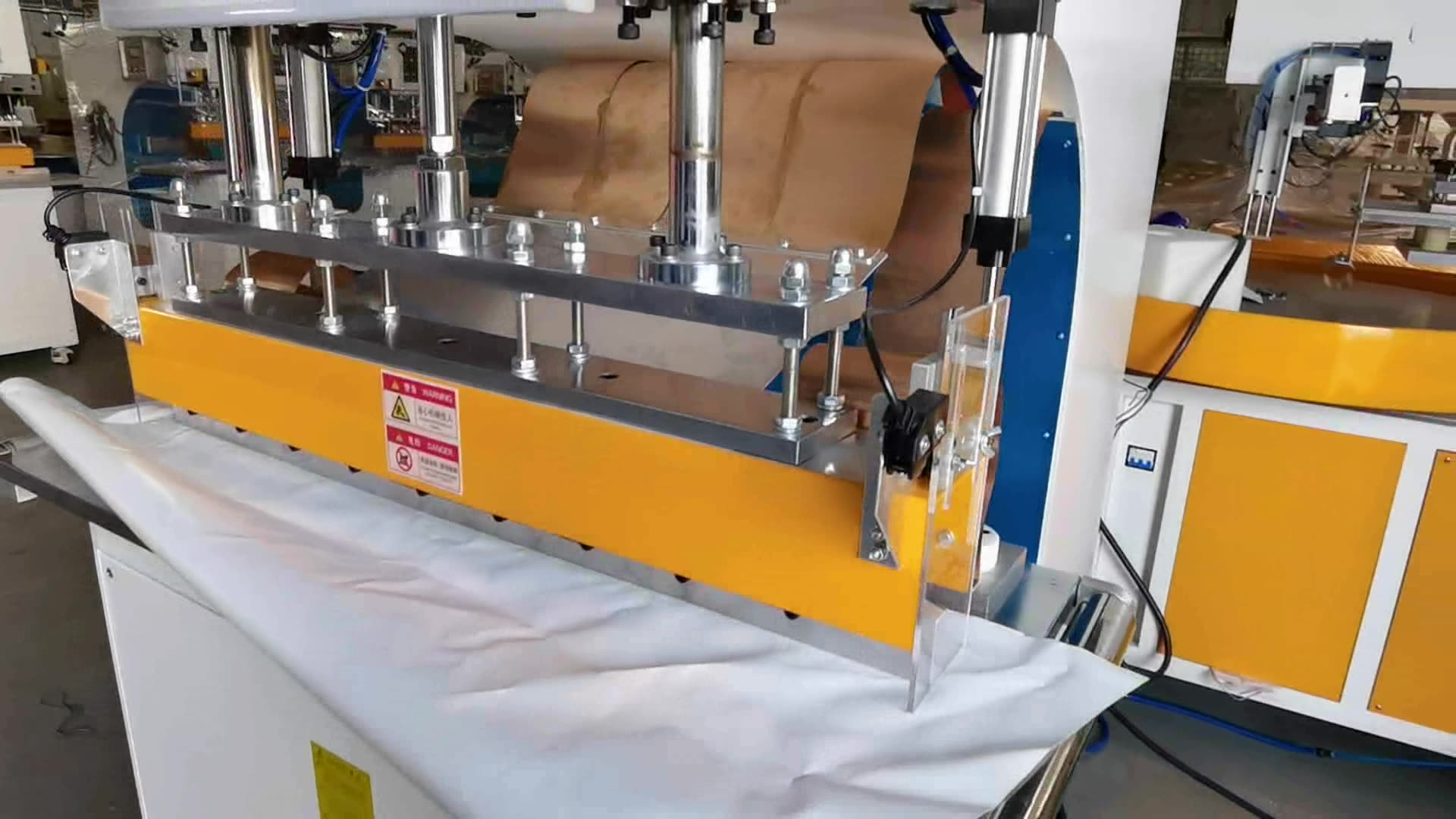
Benefits of Radio Frequency Welding
- Precise and Consistent Results: The RF welding machine offers precise control over the heat generated, making it ideal for products that require consistent and repeatable welds.
- Fast Process: Compared to traditional heat sealing or other welding methods, RF welding is quicker and more efficient. This is especially beneficial in high-volume manufacturing environments.
- Strong Bonds: The process creates durable, long-lasting welds, which are essential in industries where product integrity and durability are critical, such as medical device manufacturing.
- Minimal Thermal Damage: The dielectric welding mechanism of RF welding minimizes thermal damage to surrounding areas. This is particularly important for sensitive materials that might be affected by excessive heat.
- Versatility with Materials: RF welding can be used with a wide range of materials, including PVC, PTFE, ETFE, and PU. The technology also accommodates different thicknesses and shapes, making it suitable for various industries.
- Automation-Friendly: The welding machine can be easily integrated into automated production lines, improving productivity and reducing labor costs.
Types of RF Welders
There are several types of RF welders, each suited for different applications:
- Bench-top RF Welders: These are compact, manual machines designed for small-scale or prototype production. They are ideal for research and development or low-volume manufacturing.
- Inline RF Welders: These machines are designed for high-volume production and are usually integrated into automated assembly lines. They offer consistent and rapid welding for larger batches of products.
- Rotary RF Welders: A rotary RF welder is designed for continuous operation. The workpiece is placed in a rotating fixture, allowing multiple welding points to be processed simultaneously.
- Hand-held RF Welders: Used in specialized applications where large machines are impractical, hand-held RF welders offer flexibility for welding in tight or hard-to-reach areas.
Key RF Welding Equipment
Several essential components make up the RF welding equipment. Understanding each part is key to selecting the right machine for your application.
- RF Power Supply: The heart of any high-frequency welder, the power supply generates and controls the electromagnetic waves that cause the welding process.
- Welding Dies: These are custom-designed tools that apply pressure to the material during welding. The design of the dies ensures that the materials are properly aligned, resulting in a clean and consistent weld.
- Electrodes: Electrodes are used to transfer the radio frequency energy to the plastic materials. The design and material of the electrodes play a significant role in the effectiveness of the welding process.
- Pressure System: To ensure proper bonding, the sealing dies apply pressure to the plastic as it melts. The pressure system is designed to maintain a consistent force during the welding process.
- Cooling System: After the plastic melts and bonds, a cooling system helps solidify the weld. This cooling process is crucial to ensure that the weld retains its strength and quality.
Common Applications of RF Welding
RF welding is used in various industries due to its versatility and effectiveness. Some of the most common applications include:
- Automotive: Sealing fabrics, vinyl, and other materials used in car upholstery, airbags, and seals.
- Medical Devices: Creating strong, sterile seals in products like blood bags, IV bags, and catheters.
- Packaging: Used for producing blister packs, vacuum packaging, and other forms of plastic packaging.
- Textiles: Joining fabrics for items like inflatable products, tarpaulins, and waterproof outdoor gear.
- Electronics: Sealing electrical components or devices in protective plastic enclosures.
Common Materials Welded with RF Welding
Some of the most common materials welded with high frequency welding include:
- PVC (Polyvinyl Chloride): Widely used in packaging, medical devices, and construction materials.
- PTFE (Polytetrafluoroethylene): Known for its heat resistance and non-stick properties, commonly used in automotive and aerospace industries.
- ETFE (Ethylene Tetrafluoroethylene): Used in high-performance applications requiring chemical resistance and durability.
- PU (Polyurethane): Frequently used for soft goods such as inflatable products and outdoor gear.
Conclusion
Radio frequency welding is an advanced technology that offers significant advantages for industries that rely on joining plastic materials. Whether you are looking to weld PVC, PTFE, ETFE, or PU, the RF welding process provides a precise, reliable, and fast solution to meet your manufacturing needs. With its ability to produce strong, consistent, and durable bonds, radio frequency welding machines have become an indispensable tool in industries ranging from automotive to medical devices. Understanding the components, benefits, and applications of RF welding will help you make an informed decision when selecting the right welding solution for your business.
By investing in high-frequency welders and utilizing RF welding equipment effectively, you can enhance the quality of your products and increase the efficiency of your manufacturing process.